1. 서 론
2. 실험방법
3. 실험결과 및 고찰
3.1. Zn bath 반응
3.2. Zn bath 반응에 따른 두께 변화 및 미세조직 관찰
3.3. Zn bath 반응에 따른 Zn의 휘발
4. 결 론
1. 서 론
21세기에 있어서 자원재활용은 지구 자원․환경을 보호할 뿐만 아니라, 고갈위기에 있는 부족한 자원을 효과적․ 경제적으로 활용한다는 측면에서 매우 중요함에 따라, 최근 국내․외적으로 국가 정책적․기술적인 R&D가 활발하게 진행되고 있다. 특히 각종 산업용으로 사용 후 폐기되는 유가금속(valuable metal) 중, 특히 초경합금(cemented carbide)은 부존(賦存)이 적은 텅스텐(W)과 코발트(Co)를 주성분으로 하기 때문에 고가(高價)일 뿐만 아니라, 공업적․전략적 중요성 때문에 국내외에서 오래 전부터 재활용을 시도해 왔다1,2,3).
그러나 원래 초경합금은 고강도, 고경도 및 고융점 등의 특유한 기계적․물리적 특성 때문에 중요한 절삭공구 재료로 사용되어 왔으며, 제품의 용도 및 제조사에 따라 성능과 화학조성이 다르며, 탄화물상(WC, TaC, TiC, NbC)과 결합상의 금속(Co,Ni)의 혼합분말을 사용하여 전통적인 분말야금법(P/M법)에 의해 WC-Co계, WC-TiC-Co계 및 WC-TiC-TaC(NbC)-Co계의 3종류로 주로 제조 및 판매되고 있다. 그밖에 공구재료의 절삭능력 및 수명향상을 위해 초경합금의 모재에 고온 화학증착법을 이용하여 TiN, TIC 및 Al2O3 등의 고팅 층을 이용한 피복 초경합금(coated cemented carbide) 공구로도 제조되어 사용되고 있다. Fig. 1은 최근 국내에서 상용되고 있는 각종 초경합금 공구의 모습을 나타낸 것이다.
한편 이러한 초경합금의 재활용 방법으로 오래 전부터 시도되어 온 염화처리법은 설비에 필요한 고비용이 요구될 뿐만 아니라 저효율과 폐산/폐수의 발생에 따른 환경문제 등이 문제점으로 지적되어 왔다. 그 후 1980년대 초에 개발된 아연 욕 프로세스(Zn bath process, 이하 Zn bath 프로세스로 약한다.)는 폐산/폐수의 발생의 발생되지 않고, 처리비용이 비교적 저렴하고 초경합금원료로 재사용이 가능하다는 장점 때문에 선진 외국에서는 오래 전부터 효율적인 재활용법으로 활용되어 왔다4,5,6,7,8).
Table 1 및 Fig. 2는 국내․외에서 상용 시판되는 각종 초경합금 공구제품의 조성범위와 본 실험을 위해 국내에서 수집한 각종 폐초경합금 스크랩 사진을 나타낸 것이다. 특히 폐기된 폐초경합금을 재활용하기 위해서는 다양한 화학조성, 모양 및 크기 등이 다르기 때문에 이종금속의 분리, 합금조성의 분류 및 전처리 등이 중요하다.
Table 1.
Range of composition on the commercial cemented carbides
Elements | WC | TaC | TiC | NbC | Co |
Chemical Composition | 80~97 | - | - | - | 3~20 |
90~92 | 1~2 | - | 0.2~0.5 | 6~7 | |
70~80 | 5~8 | 3~11 | 1~3 | 6~13 | |
80~85 | - | 3~4 | - | 13 | |
80~82 | 2~3 | - | - | 15 |
따라서 본 연구는 Zn bath 프로세스를 이용하여 현재 국내에서 사용 후 폐기되고 있는 폐초경합금을 재활용할 수 있는 기초적인 데이터를 확보하기 위해 폐초경합금과 용융 아연의 반응에 있어서 중요한 아연첨가량, 반응온도 및 시간, 그리고 아연 증발 손실 등을 조사하였다.
2. 실험방법
Fig. 3은 본 연구에서 사용한 실험장치의 개략도를 나타낸 것이다. 본 연구에 사용한 폐초경합금 스크랩은 Table 1 및 Fig. 2에서 알 수 있는 바와 같이, 다양한 화학적 조성, 형상 및 크기로 혼재되어 있어 본 실험에서는 가능한 동일한 조성 및 크기의 WC-TiC-TaC-Co계의 인써트 팁(13x 13x3(mm))을 선별하여 사용하였다. 화학적 조성비는 SEM/ EDS에 의한 정성적 분석한 결과 68.7%W-7.5%Co-6.6%Ta- 7.9%Ti-2.1%Nb이었다. 폐초경합금 스크랩과 아연 잉곳 시료의 질량비는 Co-Zn 2원계 평형상태도로부터 약 700℃에서 Co와 Zn의 액상반응을 위해 6:94정도로 추정되어, 실제로 초경합금과 아연은 6.8g:11.70g(=1:1.72)의 비율로 천평하여 실험하였다. 아연은 순도 99.9% 이상 잉곳을 사용하였으며, 천평된 시료는 석영제 도가니(∅15x60mm)에 장입하여 튜브전기로를 사용하여 Ar분위기에서 700~ 900℃x(1~3)h 동안 가열한 후, 재차 900~1100℃범위로 승온시켜 2.5x10-3torr 이상의 진공분위기에서 0.5~1.5h 동안 가열하였다. 얻어진 시료 중 일부는 아연 증발율(%)을 조사하기 위하여 전자전울로 천평하였으며, 폐초경합금 스크랩의 두께 측정 및 상분석을 위해 와이어 커팅 후 수지에 마운팅하여 연마하여 SEM/EDS으로 분석하였다.
3. 실험결과 및 고찰
보통 Zn bath 프로세스를 이용하여 WC-TiC-TaC-Co계 폐초경합금을 재생할 경우, 아래와 같이 (1) Zn bath 반응 및 (2) Zn의 증발 2단 단계로 구분하여 예상할 수 있다.
본 연구에서는 이러한 반응을 토대로 하여 Zn bath 프로세스에 따른 주요 반응기구를 조사하기 위해 몇몇의 기초실험과 고찰을 행하였다.
3.1. Zn bath 반응
Fig. 4에 나타낸 Co-Zn 2원계 평형상태도9)에서 추측할 수 있는 바와 같이, 초경합금 스크랩과 금속 아연(Zn)을 접촉시켜 아연 융점(420℃) 이상으로 가열하면, Zn 측에 존재하는 γ, δ, γ1 및 γ2 등 다수의 Co-Zn계 금속간 화합물이 생성될 것으로 예상되며, 실제로 Zn bath 반응 시 Co와 Zn의 액상반응과 아연휘발을 고려하면, 폐초경합금과 아연의 중량비는 1 : 1.72 이상 필요할 것으로 추정된다.
Fig. 5은 본 연구에서 폐초경합금과 순 금속아연의 질량비를 1:1.72로 준비하여 DSC로 분석한 결과이다. Zn의 융점(420℃) 부근에서 처음 나타난 흡열 peak는 순금속 아연의 용융에 의한 peak로 판단되며, 이어서 640℃부근에서 나타나는 흡열 peak는 Fig. 4의 Co-Zn 2원계 평형상태도에 존재하는 γ2 및 γ1상의 형성에 따른 peak인 것으로 판단되었다. 또한 750℃부근의 peak는 δ상, 900℃부근에서 관찰된 peak는 γ상의 형성에 따른 peak로 추정되었다.
이상의 Co-Zn 2원계 평형상태도 분석 및 DSC 분석 등의 결과는 Zn bath 프로세스에 의한 초경합금의 재활용 시, 금속아연의 첨가량, 가열온도 및 시간 등에 따른 반응속도의 추정을 위해 기초자료가 될 것으로 판단된다.
3.2. Zn bath 반응에 따른 두께 변화 및 미세조직 관찰
Fig. 6 및 Fig. 7은 본 연구에서 폐초경합금(WC-TiC- TaC-Co계) 스크랩을 700℃에서 반응시간을 0.5~2.0h까지 변화시켜 실험한 시료를 절단하여 수지에 마운팅하여 단면을 연마하여 일부의 시료를 SEM 및 EDX로 관찰 및 분석한 결과이다. 이러한 실험결과 700℃에서 실시한 반응시간 증가에 따라 폐초경합금(WC-TiC-TaC-Co계) 스크랩의 두께가 선형적으로 감소함을 알 수 있었다. 이러한 결과는 Zn bath 반응 중 Zn의 첨가량이 부족했거나 Zn가 휘발되어 Co-Zn의 반응속도에 영향을 주지 않은 것으로 판단된다. 그러나 Zn bath 반응을 800℃이상의 온도에 가열하거나, 2시간 이상 가열할 경우에는 Zn 첨가량이 더욱 필요할 것으로 판단되었다.
Fig. 8 및 Table 2는 Fig. 6-(d)에 나타낸 시료를 EDX로 점분석 및 선 분석한 결과로서, 탄화물 상과 Co-Zn alloy 2개의 상으로 관찰되었다. 이러한 2개상의 분리 및 거동은 예상했던 바와 같이, 고상의 초경합금과 용융아연의 계면에서 결합제(binder)로 함유된 고상의 Co와 우선적으로 반응이 시작되어 Co가 용출되거나 초경합금 내로 Zn이 침투하는 확산반응에 의해 Co-Zn합금이 생성됨과 동시에 WC-TiC-TaC-Co계 탄화물이 2상(phase)으로 분리되는 것으로 추정되며, 동시에 부피팽창이 일어나 붕괴되는 것으로 파악되었다.
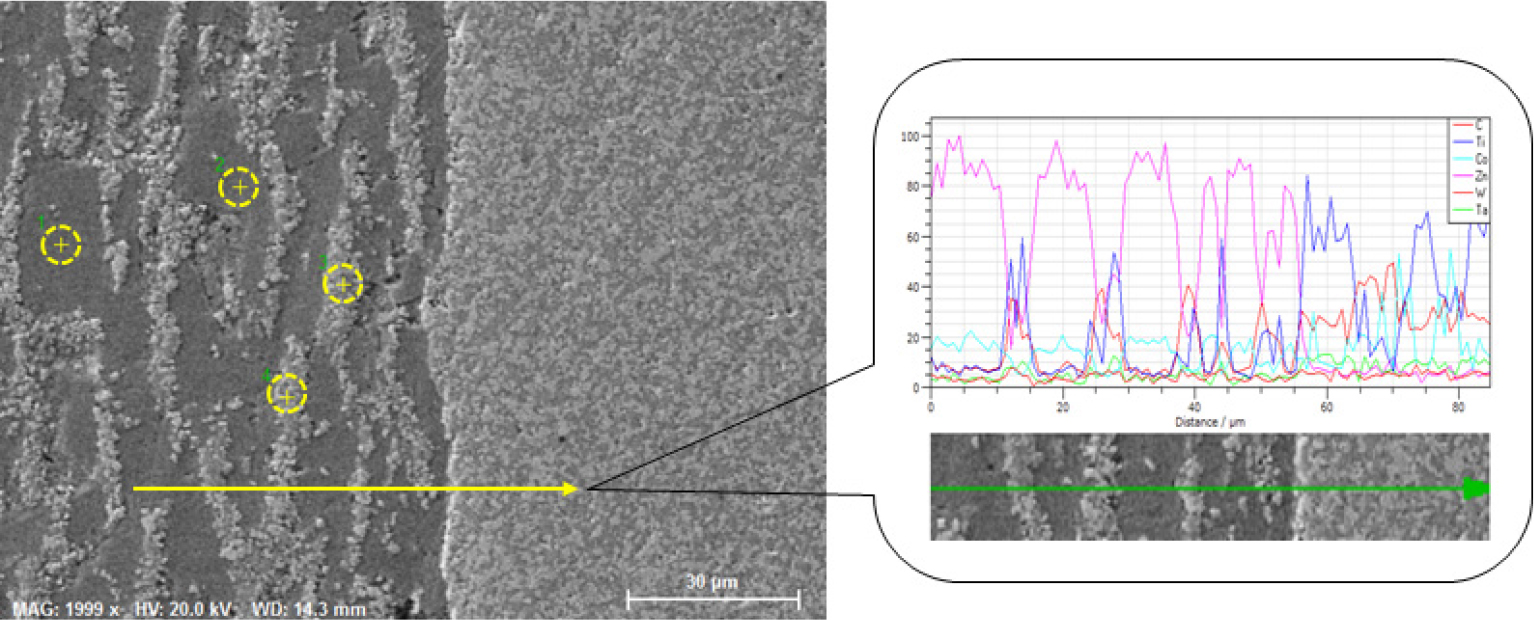
Fig. 8
Results of EDX analysis of sample prepared by a reaction for 2h at 700℃(Fig. 6-(c)) by Zn bath process.
Table 2.
Results of EDX point and line analysis of sample prepared by a reaction for 2h at 700℃ by Zn bath process
chemical compositions(wt%) | rep. | ||||||
No. | Co | Zn | Ti | Ta | W | C | |
1 | 7.72 | 92.28 | - | - | - | - | |
2 | 7.77 | 92.23 | - | - | - | - | |
3 | - | 16.40 | 2.35 | - | 71.29 | 9.96 | |
4 | - | 20.91 | 15.44 | 11.14 | 38.60 | 13.92 |
3.3. Zn bath 반응에 따른 Zn의 휘발
Zn bath 프로세스에 있어서 첨가하는 아연은 비등점이 907℃로 비교적 낮을 뿐만 아니라, 증기압이 높기 때문에 반응온도가 비등점 이상으로 너무 높을 경우에 Zn이 휘발되어 Co-Zn계 액상반응이 진행되지 않기 때문에 적절한 물리적/화학적 반응조건의 조사가 중요하다.
Fig. 9는 본 연구에서 Zn bath 반응 시 Zn 휘발정도를 조사하기 위해 반응온도를 700℃에서 3시간 Zn bath 반응 후, 계속하여 3.0x10-2 torr로 진공상태를 유지함과 동시에 가열시간을 1h으로 고정하고 반응온도를 800~1100℃로 승온시켜 가열 및 냉각하여 얻어진 시료의 무게를 전자저울로 측정하여 Zn의 휘발정도를 백분율(%)로 나타낸 것이다.
그 결과 Fig. 9에서 알 수 있는바와 같이, 700℃에서 3시간의 Zn bath 반응 후에는 52.3% 잔존하였다. 그 후 진공상태에서 반응온도의 상승에 따라 Zn의 휘발은 크게 증가하였으며, 특히 Zn 비등점(907℃)이상에서는 크게 증가하여 1100℃에서는 99.2% 이상 휘발됨을 확인하였다. 한편 Co의 비등점은 2900℃이므로 Co 휘발은 거의 없을 것으로 판단된다.
4. 결 론
본 연구는 Zn bath 프로세스에 의한 폐초경합금 스크랩의 재활용 시 중요한 반응온도 및 시간, 아연 첨가량 등을 조사하기 기초실험을 진행하였으며, 그 결과를 요약하면 다음과 같다.
[1] 폐초경합금 중의 Co함유량을 파악하여 Zn와의 액상반응 및 Zn의 증기압을 고려하여 Co-Zn 2원계 상태도로부터 추정하여 폐초경합금 중의 Co함유량과 금속 Zn의 중량비는 1 : 1.72 정도가 요구되는 것으로 파악되었으며, 실제로 700℃에서 0.5~2h동안 실험한 결과 반응시간 증가에 따라 폐초경합금 스크랩 시료의 두께가 선형적으로 감소함을 알 수 있었다.
[2] Zn bath 반응에 따른 DSC분석에 의한 420℃, 640℃, 750℃ 및 900℃부근에서 관찰된 4개의 흡열 peak, 즉, 420℃부근 peak는 Zn의 융점, 그 밖에 peak는 Co- Zn 2원계 평형상태도에서 관찰되는 γ2 , γ1 및 δ상 등의 형성에 따른 것으로 판단되었으며, 보다 상세한 고찰을 위해서는 XRD분석 등 다양한 보충실험이 필요한 것으로 판단되었다.
[3] Zn bath 반응 시, Zn 휘발은 700℃x3h의 Zn bath 반응에서는 52.3%정도가 일어났지만, 계속하여 진공상태(3.0x10-2torr)에서 1h동안 승온하면 Zn 비등점(907℃) 이상에서 크게 증가하였으며, 1100℃에서는 99.2% 이상 증발됨을 확인하였다.