1. 서 론
2. 전해 기반 마그네슘 회수 기술
2.1. 양이온교환막 기반
2.2. 음이온교환막 기반
2.3. 복합막 기반
2.4. 비막 전해(Membraneless Direct Electrolysis)
3. 시사점 및 전망
4. 결 론
1. 서 론
마그네슘(Mg)은 알루미늄 합금과 다이캐스팅에 많이 쓰이며, 탈황제 등 화학이나 의약품 분야에서도 많이 쓰인다1,2,3). 또한 최근에는 마그네슘의 가벼운 중량과 높은 이온화경향을 이용하여 배터리의 원료로서도 연구되고 있다4). 참고로, 미국의 경우 2019년 천연 해수와 염수에서 추출되는 마그네슘이 그 해 미국 내 생산되는 전체 마그네슘의 약 73%를 차지하였으며, 생산 가치는 3억달러에 가깝다고 추산되었다. 그 외 마그네사이트 등에서 마그네슘 혹은 관련 화합물을 생산하기도 하였다. 미국 내 유통되는 마그네슘 화합물의 70% 이상은 염화마그네슘, 수산화마그네슘 또는 황산마그네슘의 형태로 농업, 화학, 건설, 제빙, 환경 및 산업 등 다양한 분야에 소비되었으며, 나머지는 내화물로 활용되었다. 전세계에서는 중국이 마그네슘의 주요 생산국으로 중국의 정책 변화가 마그네슘의 가격과 경제적 측면에 큰 영향을 미치고 있는 실정이다. 그 외에 터키, 브라질 및 러시아에서도 생상된다5). 참고로 Figs. 1-2에 2021년 국가별 마그네슘 생산량(Fig. 1)과 대표적인 마그네슘 함유 광석인 마그네사이트의 2023년 매장량(Fig. 2)을 비교하였다. 특히, Fig. 2의 경우 국가별 매장량과 함께 지구 전체 해수에 용해되어 있는 마그네슘 이온의 중량 값을 추정하여 도시하였다6,7). 마그네슘은 지역 및 연도별 가격 차이는 있지만, 수산화마그네슘 원자재의 경우 대체로 미국이나 중국 등지에서 톤당 1000불 정도에 판매되고 있으나 순도 별로 큰 차이가 있다8).
마그네슘은 주로 광석이나 염수/해수에서 추출가능하며, 후자의 경우 침전 및 결정화 등을 통해 마그네슘을 회수될 수 있다5). 이 중 산염기 반응 기반 침전은 현재 염수 내 마그네슘 회수에 보편적으로 적용되는 기술이다1,5). 마그네슘 침전을 위해서 수산화나트륨이나 소석회 등 다양한 침전제가 사용된다1). 다만 침전은 다량의 약품이 주입되어야 하며 그에 따른 경제적 비용 및 기술적 부담이 따른다9). 한편, 전해 반응을 통해 해수나 염수에서 마그네슘을 추출할 수도 있는데, 이 기술은 외부 전력만 효율적으로 주어진다면 별도의 첨가제 없이 수산화마그네슘 침전물 같은 형태로 회수가 가능하기 때문에 주목할 만하다9). 다만, 이 시점에서 전해기반 마그네슘 회수 관련 실험연구의 동향 리뷰 및 향후 전망 제시가 검토될 필요가 있다. 따라서, 본 연구에서는 전해를 통한 마그네슘 회수 기술을 장착된 막의 종류에 따라 양이온교환막9,10,11), 음이온교환막12,13), 전기투석14) 및 비막기술15)로 분류하고 이에 대한 각 메커니즘을 파악하였다. 그리고 관련 최근 연구 동향 검토 및 향후 연구 방향을 제시하였다.
2. 전해 기반 마그네슘 회수 기술
2.1. 양이온교환막 기반
마그네슘 전해액에 함유된 경우, 양극과 음극 간 전류를 가하면 아래의 전해 및 침전 반응이 발생할 수 있다9).
양극 측:
음극측:
상기와 같이 양극액에서는 수소이온이 생성되고, 음극액에서 생성된 수산화이온이 마그네슘 양이온과 결합하면서 수산화마그네슘으로 침전된다. 이 때 양이온교환막은 양극액 내 마그네슘 이온을 음극액으로 전달하거나 음극액의 수산화 음이온 이동을 억제하여 수산화마그네슘의 침전율 제고에 기여하는 역할을 한다.
기존의 한 연구에서는 황산나트륨 용액을 양극액으로, 마그네슘, 칼슘, 나트륨 등이 포함된 해양심층수를 음극액으로 하였다9). 양극 내 물분자의 전해반응으로 생성되는 수소 이온 농도에 비해 황산나트륨 수용액의 농도가 높기 때문에 나트륨 이온이 양이온교환막을 통해 음극액으로 이동되는 대신, 수소 이온의 이동 및 그로 인한 음극액 내 산염기 중화도 억제되어 음극액 내 수산화 이온 농도 증가 및 수산화마그네슘 침전이 활발하게 진행될 수 있었다(Fig. 3 참조). 그리고, 음극액 내 수산화이온 및 그에 따른 수산화마그네슘 생성량은 외부 전력에 의한 전류에 비례한다고 보고하였다9).
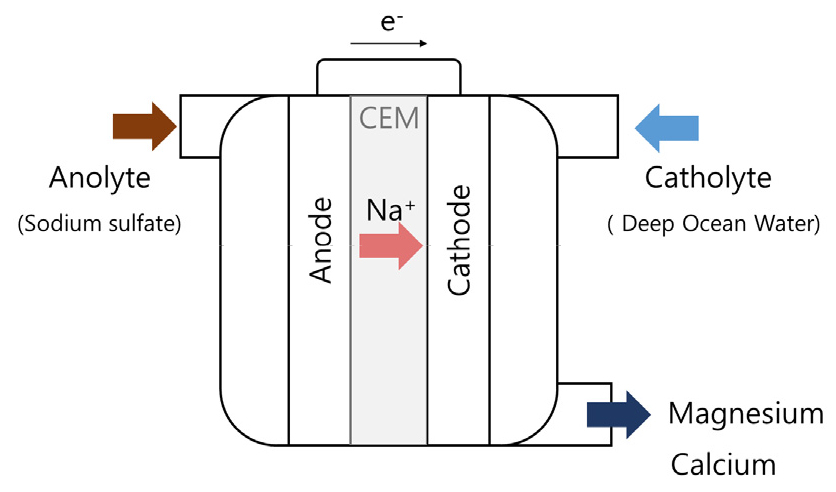
Fig. 3.
A schematic demonstration of the magnesium recovery using the electrolysis with a CEM (Cation-Exchange Membrane)9).
참고로, 수산화이온이 마그네슘 외 해수 내 다른 양이온과도 반응할 수도 있는데, 이 때 수산화마그네슘의 용해도는 음극액에서 생성가능한 다른 수산화침전물인 수산화칼슘이나 수산화나트륨에 비해 매우 낮다. 따라서 음극액에서 생성되는 수산화이온은 주로 마그네슘 이온과 반응한다고 볼 수 있다. 다만, 음극액 중에 탄산염이 다수 존재할 경우 이들이 칼슘과 반응하여 불용성 탄산칼슘이 생성될 수 있으며 이들이 공침할 경우 수산화마그네슘의 순도를 저하시킬 수 있을 것이다. 이에 해당 연구팀은 음극액인 해양심층수에 탈기를 가하여 이산화탄소를 제거하면 탄산칼슘 생성이 방지되어 고순도(99%)의 수산화마그네슘이 생성될 수 있다고 하였다9). 이 후 침전에 의해 액중 마그네슘 이온이 고갈되면 잔류 수산화이온은 칼슘과 반응하여 고순도의 수산화칼슘이 생성될 수 있다. 이러한 방법으로 생산된 수산화마그네슘의 비용은 기존 방법에 비해 저렴하다고 보고하였다.
한편 Pan et al.의 연구에서는 염소, 마그네슘 및 리튬이온이 함유된 인공 염수로부터 고순도 마그네슘과 리튬을 효율적으로 분리하기 위한 다단계 막전해 공정을 제안하였다10). 이 연구가 제시한 (3단) 다단막전해 공정은 1단 전해공정을 4시간 후에 중지시키고 해당 1단에서 배출된 양극액과 (수산화마그네슘 침전물을 여과분리하고 남은) 음극 여과액을 다음 2단계 전해공정의 양극액과 음극액으로 사용하였다. 3단도 마찬가지로 2단에서 배출된 용액을 전해액으로 사용한다. 그 결과, 양극액 내 마그네슘의 침전회수를 통해 Mg/Li 질량비는 초기 98에서 0.17로 크게 감소하였다. 한편, 다단 전해 공정을 통해 높은 마그네슘 회수율(98.86%) 및 순도(99.93%)를 달성하였다10). 이후 해당 연구그룹은 염소, 마그네슘 및 리튬 외에도 추가적으로 나트륨, 칼륨, 붕소 등이 함유된 희석 인공염호를 양극액으로, 염화리튬을 음극액으로 하여 마그네슘을 전해회수하였다11). 그 결과 마그네슘 회수율 90.62%이 달성되었고, 여타 금속 양이온의 분리율은 90.59%에 달하였다. 회수된 수산화마그네슘은 바로 난연제의 원료로 사용될 수 있을 정도로 순도가 높다고 보고되었다11).
2.2. 음이온교환막 기반
전술된 양이온 교환막 기반 전해회수와는 달리 Xie et al.은 음이온 교환막을 이용하여 마그네슘을 회수하였다12). 참고로 이 연구에서는 다양한 농도(0–1.6 M)의 염산을 양극액으로, 염화마그네슘 용액(1 M)을 음극액으로 사용하였다. 사실 이 연구의 주 목적은 용액에 (20%–100%의 고농도) 이산화탄소 기체를 최대한 흡수/제거하는데 있었다12). 이 때 음이온 교환막은 수산화마그네슘과 수소이온 혼합 방지와 음극액의 염소이온 이동/제거에 유용하다(Fig. 4 참조). 이는 (원래 유입시에는 염화마그네슘이) 포함된 염기성 음극액에 이산화탄소가 최대한 흡수되어 가능한 많은 마그네슘이 탄산마그네슘으로 전환되고 염소이온은 음극액에서 제거되어야 하기 때문인 것으로 보인다. 만일, 양극액의 수소이온이 염기성 음극액에 유입되면 음극액 pH 및 그에 따른 이산화탄소 흡수율이 저하될 수 있다. 또한 염화마그네슘에서 분리된 염소이온이 음극 내 체류한다면 이산화탄소에서 전환된 탄산염 이온과 음이온 간 경쟁에 놓여질 우려가 있는 것이다. 여하튼 이들의 실험 결과, 염화마그네슘이 먼저 전기분해에 의해 수산화마그네슘으로 전환된 후, 상당량의 수산화마그네슘이 고농도의 탄산에 의해 magnesite나 nesquehonite 같은 유용한 탄산염 광물로 전환/회수되었다12). 염화마그네슘의 전기분해는 0.60 V 정도의 전압에서 이루어졌는데, 실제 셀 전압은 0.7 V였다. 0.1 M의 염산 양극액 당 3.16톤의 nesquehonite를 생산되었으며 이산화탄소 1톤을 광물화시키는데 필요한 에너지는 약 871 kWh였다. 이 후 해당 연구자들의 다음 연구에서는 에서의 전해실험에서는 약 1.3 V의 전압 기반 1000 m3의 농축 해수를 이용하여 4.65톤의 이산화탄소를 광물화할 수 있었다. 또한 총 5676 kWh의 전력으로 탄산마그네슘 9.97톤, 침강성 탄산칼슘 2.02톤을 생산하였다13).
2.3. 복합막 기반
지금까지는 해수나 염수에서 침전물의 형태로 마그네슘을 회수한 반면, 다중막 기반 전기투석 방식을 이용하면 마그네슘을 이온의 형태로 농축시킬 수 있다. 여기서, 문제는 해수나 원수 내 다른 여러 이온의 존재, 특히 나트륨 1가 양이온이 상대적으로 고농도로 존재한다는 점이다. 따라서 이온교환막 이용시 나트륨 이온 대비 마그네슘 이온을 선택적으로 이동시켜 농축 및 배출시키는 어려움이 제기될 수 있다. 이를 위해 Ghyselbrecht et al.은 기존의 전기투석 스택에 1가 선택적 양이온교환막을 보조적으로 장착한 양이온 선택투석(cSED: cationic Selectrodialysis)을 고안하였다14). 1가 선택적 양이온교한막은 전술하다시피 나트륨/마그네슘 이온 분리를 위한 것이다14). 먼저 (1) 원수(해수 혹은 염수)를 cSED stack의 음극 쪽으로 주입하여 음이온(거의 염소이온)이 전기장을 따라 음이온 교환막을 통과하여 양극방향으로 이동하게 하고 나머지 이온(대부분 나트륨이나 마그네슘 양이온)은 (1차 처리수) 수중에 잔류한채로 cSED에서 배출시킨다. (2) 배출된 1차 처리수를 cSED의 양극 쪽으로 주입하여 수중의 양이온을 양이온교환막을 통과하여 음극 방향으로 이동시킨다. 이때 음이온은 양이온 교환막을 통과 못하고 2차 처리수 내에 잔류하게 된다. (3) 한편 양이온교환막을 통과한 (나트륨과 마그네슘 등) 양이온은 전기장의 영향으로 음극쪽으로 계속 이동 하는데 이동경로에 1가 양이온만 이동시키는 특수 양이온교환막을 설치하여 나트륨은 음극방향으로 투과되지만 마그네슘 등 2가 이온은 투과가 불가하다. (4) 결국, 마그네슘은 이온 형태로 회수물에 수집되고 나트륨과 염소이온은 Brine으로 수집되며 원수는 탈염수로 배출되는 방식이다. Fig. 5에 상기 처리 과정을 도시화하였다.
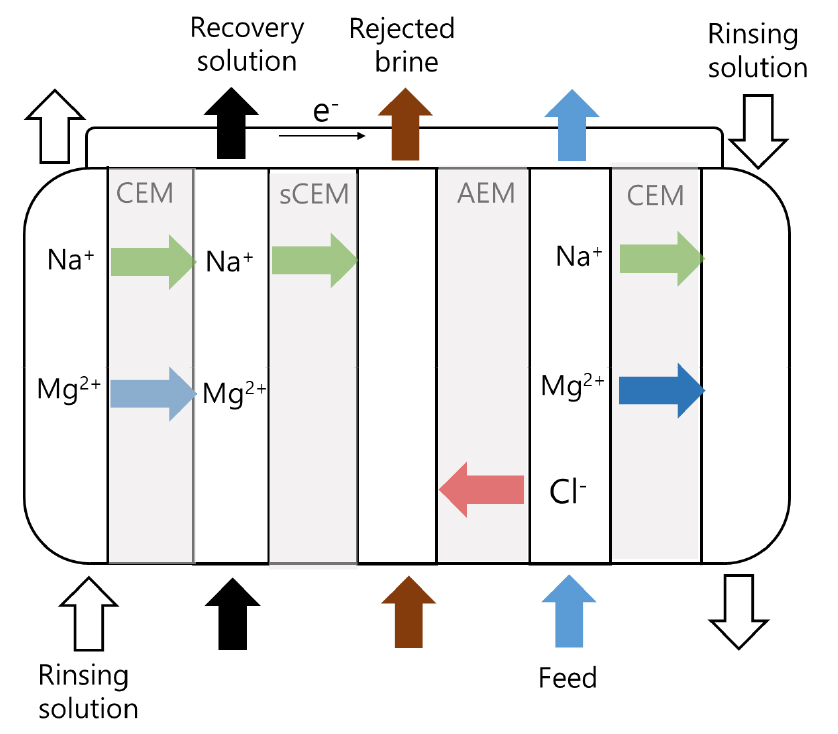
Fig. 5.
A schematic demonstration of the magnesium recovery using the electrodialysis with a set of CEM + sCEM (Monovalent Selective Cation-Exchange Membrane) and AEM (Anion-Exchange Membrane)12,13). Inlet solutions containing various properties as rinsing solution (0.5M NaNH2SO3), Recovery (0.25–1 M NaCl), Rejected brine (0.5 NaCl), and Feed (synthetic or real seawater)14).
마그네슘이 함유된 인공 (북해)해수를 원료로 하여 상기 선택투석을 통한 마그네슘 농축 실험 결과, 상대적으로 낮은 전류밀도(100 A/m2 vs. 300–500 A/m2)에서 상대적으로 고농축된 Mg2+가 회수물(Product)에서 얻어졌다14). 또한 원수 내 초기 염화나트륨(NaCl) 농도가 0.5 M에서 절반 정도로 저하되었을 때 비회수 구획에서의 마그네슘 농도가 증가하는 부적절한 결과가 관측되었다14). 이는 아마도 전하수지에 기반한 문제로 보이며 동종(양)이온의 농도가 증가하면 일부 양이온의 이동이 활발해지지만 그렇지 않을 경우 이동이 지체될 여지가 있기 때문일 것이다. 참고로 회수물 내 칼슘 농도도 증가하였는데 이는 해당 연구의 취지 상 상기 선택투석의 선택성이라는 개념이 마그네슘과 타이온이 아닌 음이온 혹은 1가 양이온 대비 2가 양이온(마그네슘 및 칼슘) 간의 선택성을 증진시키는 의도이기 때문인 것으로 보인다.
2.4. 비막 전해(Membraneless Direct Electrolysis)
전해회수는 일반적으로 이온교환막이 수반되며 이는 투자 및 운전비용의 상승을 야기시키는 주 원인 중 하나이다. 따라서 이온교환막 없는 전해회수공정(직접전해)을 고안할 수 있다면 회수비용을 저감시킬 수 있음을 기대할 수 있다. Lalia et al.의 연구에서는 이러한 직접 전해를 통해 칼슘 대비 마그네슘을 선택적으로 침전-회수하는 실험을 수행하였다(Fig. 6 참조)15). 특히, 염수 기반 전해 시 침전 선택성을 강화하기 위해 이산화탄소 가스 Purging을 포함한 새로운 2단계 공정을 제시하였다15). 첫번째 단계는 2.5 V의 전위에서 Titania 코팅 흑연 음극과 순수 흑연 양극을 사용하여 칼슘을 탄산칼슘(방해석 형상)으로 침전시키기 위하여 염수에 이산화탄소를 Purging한다. 두번째 단계에서는 방해석 제거 후 3.5 V의 전위에서 깨끗한 흑연 음극과 양극을 사용하여 마그네슘을 브루사이트 형태로 석출시켰다. 첫번째 단계 후 Purging을 중지하고 전위를 2.5 V 이상으로 상승시키면 수산화이온 농도 증가 및 침전으로 인해 액중 마그네슘 이온 농도가 상대적으로 급격히 감소하기 시작하였다. 반면, 칼슘 이온 침전은 이산화탄소 및 탄산염 이온 부족으로 인해 제한되었다. 즉, 이산화탄소 Purging은 2.5 V에서 브루사이트 침전을 억제하고 방해석의 선택적 침전에 도움이 되었다15). 이러한 비막 기반 마그네슘 전해 회수 연구는 흥미롭지만 아직 기초 단계로 순도 및 효율을 최적화하기 위한 연구가 더 필요한 실정이다. 참고로 본 연구에서 검토한 전해 기반 마그네슘 회수 실험 결과를 Table 1에 요약하였다.
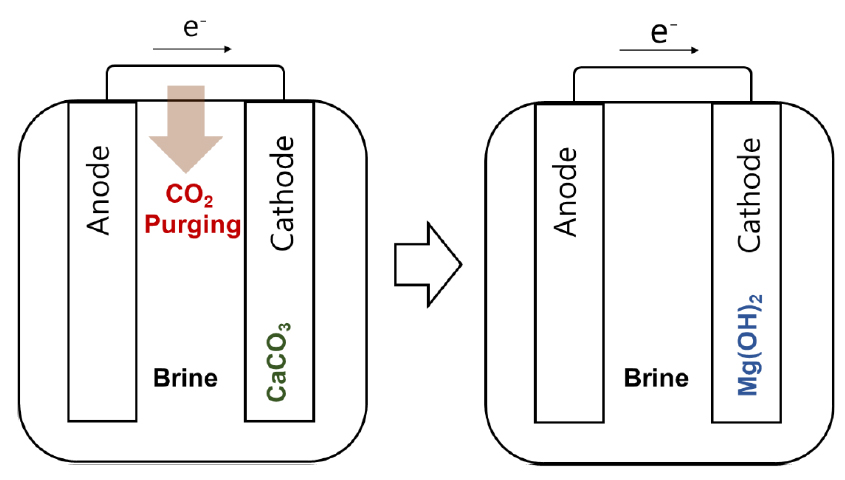
Fig. 6.
A schematic demonstration of the magnesium recovery using the membraneless direct electrolysis with CO2 purging15).
Table 1.
Details of magnesium recovery technologies based on electrolysis
Reference | Recovery eff. | Purity | Voltage |
Current (density) | Membrane | Feed | Electrodes & Electrolytes | Memo | |
Sano et al. (2018) | 100% as Mg(OH)2 | 99% | 5-6 V* |
100-1200 A/m2 (1.2-14.4 A) |
CEM (CMB, ASTOM, Japan) |
Deep-ocean water (1.173 g/L of Mg2+ conc.) |
Cathode: platinized titanium plate Catholyte: deep-ocean water |
Anode: platinized titanium plate Anolyte: 5% sodium sulfate |
Deaeration to the deep-ocean water was heilpful for CO2 removal and thereby preventing CaCO3 formation |
Pan et al. (2020a) |
99% as Mg(OH)2 in < 6 hrs |
close to 100% |
around 4 V* |
2.4 A (300 mA/cm2) |
CEM (Hefei ChemJoy Polymer Mateterials Co., Ltd.) | Artiificial solution |
Cathode: pure titanium plate Catholyte: Li+ (8.2 g/L), Cl- (41.87 g/L) |
Anode: titanium plate coated with metal oxide Anolyte: Mg2+ (25.54 g/L), Li+ (2.26 g/L), Cl- (76.07 g/L) |
A novel multistage electrolysis to separate Mg:Li from brines |
Pan et al. (2020b) |
91% as Mg(OH)2 in 2 hrs |
close to 100% | 8-11 V |
1.5 A (201 mA/cm2) |
CEM (Hefei ChemJoy Polymer Mateterials Co., Ltd.) |
Artifical saline lake brine (19.4 g/L-Mg2+ of anolyte; 84.2 g/L-Mg2+ of brine) |
Cathode: pure titanium plate Catholyte: 1. MgCl2 2. LiCl |
Anode: titanium plate coated with IrO2 Anolyte: 1. MgCl2 2. simulated brine |
Precipates similar to pure magnesium chloride electrolysis products |
Xie et al. (2014) | N.A. | N.A | 0.6-1.5 V | 0-60 A |
AEM (China Iontech co.) | Artificial solution |
Cathode: Nickel foil Catholyte: MgCl2 (1M) with NaCl |
Anode: Hydrogen gas diffusion electrode Anolyte: Hydrochloric acid (0-1.6 M) |
Mg(OH)2 transformed to MgCO3 via. CO2 flue gas |
Ghyselbrecht et al. (2019) |
(LAB operation) Overall > 85% of Mg2+ decrease in 3 hrs | N.A |
around 18 V (< 30 V) |
100, 300, 500 A/m2 |
Standard AEM (PC-SA) Monovalent sCEM (PC-MVK) Standard CEM (PC-SK) End CEM (PC-SC) (PCA - PolymerChemie Altmeier GmbH, Heusweiler, Germany) |
Synthetic or Real North Sea water: 1.1~1.2 g/L of Mg2+ conc. |
Dilute: Synthetic or real seawater Brine: 0.5 M NaCl solution Product: 0.25, 0.5, 1 M NaCl solution ERS: 0.5 M NaNH2SO3 |
Cationic selectrodialysis (cSED): A lower current density resulted in a higher Mg2+ concentration in the product. | |
(Pilot operation) Batch: 83% of Mg2+ decrease in 3 hrs F-B: 31% decrease | 300 A/m2 |
Dilute: Seawater Brine: 0.5 M NaCl solution or Seawater (200 L) Product: 0.5 M NaCl or Seawater ERS: 0.5 M NaNH2SO3 | |||||||
Lalia et al. (2021) |
96% as Mg(OH)2 in 3 hrs | N.A |
2.5, 3.5 V | around 1 A* |
No membrane (Direct electrolysis) |
Artifical brine (Mg2+ conc. of 2500 ppm) |
Cathode: pristine graphite | Anode: pristine graphite |
Calcite precipitated prior to brucite (Mg(OH)2) precipitation |
3. 시사점 및 전망
전해 기반 마그네슘 회수 관련 최근 연구의 동향을 보면 대체로 고농도 마그네슘 함유 해수나 염수를 원료로 하여 (양)이온교환막을 장착한 전해조에서 높은 수율 및 순도의 수산화 마그네슘 침전물 형태로 마그네슘을 회수하는 것이 일반적인 것으로 보인다. 또한, 최근 연구에서 보고된 바와 같이 일반적인 해수를 사용할 경우에도 회수의 고효율화와 더불어 높은 선택성을 유지하는 것이 가능할 것으로 보인다. 물론 향후 추가 연구를 통해 다양한 성상과 농도가 포함된 포함된 해수 혹은 염수시료를 이용, 장기간 운전을 통해 마그네슘 외에도 가능한 다수의 유가물질에 대한 회수 선택성 및 효율을 증진시키는 것은 중요할 것이다. 본 연구에서 리뷰한 선택적 전기투석 기반 해수의 탈염과 마그네슘의 동시 회수 연구는 매우 흥미롭지만 이 경우 회수최적화와 더불어 막에 투여되는 비용 및 운전관리 문제도 더 고려되어야 할 것이다16). 또한 전해 회수공정 전 나노필터 등을 통한 불순물 전처리 등의 기술 대안 등도 검토되어야 할 것이다.
학술적 측면에서 상기 기술경제적 공정최적화를 위해서 보다 모니터링 및 상세 메커니즘에 기반한 과포화-침전-회수 세부공정을 모델링 해야 한다17,18). 이를 위해서 액중 과포화도나 이에 따른 다종 이온 및 침전의 거동이 물리화학적으로 적절히 모니터링 되어야 하며 이는 pH나 전기전도도 뿐 아니라 침전물의 핵형성, 결정성장 및 응집 등 가급적 다양한 인자가 모니터링 대상 항목에 포함되도록 하는 것이 바람직하며, 침전물 순도 평가시에도 침전물 재용해를 통한 정확한 순도 측정이 병행되어야 할 것이다.
마지막으로 경제성 및 기타 측면에서는 환원극에서 발생하는 수소나 차아염소산 혹은 여타 광물을 회수할 경우 추가적인 매출을 올려 경제성을 증진시킬 수 있을 것으로 판단된다. 또한 전해액 내 pH의 양극화 및 양이온의 존재로 인한 이산화탄소의 흡수 및 저탄소화 및 전해액의 재이용/재활용 등을 병행할 수 있다면 환경성 및 추가적인 경제성 증진을 도모할 수 있다. 이러한 효율 대비 비용은 결국 전통적인 무전해 침전 회수 기술과 비교되어야 하며 특히 이는 스케일업 설계 및 장기간 운전 데이터를 통한 최적화를 전제로 해야 한다. 장기간 운전은 막의 수명 및 교체주기를 결정하는데 중요하며 이는 현실적인 운전비용 산정에 중요하다. 참고로, 이온교환막은 고비용 소재로서 전해 중 발생가능한 활성이온 등으로 인해 물리화학적 저해를 받으며 시간에 따른 성능저하가 심각하면 교체가 필요하다. 이는 전극의 경우도 마찬가지이다.
4. 결 론
해수나 염수에서 마그네슘을 추출하는 전해 반응은 외부 전력 이용, 화학약품을 사용하지 않고 주로 수산화마그네슘 형태로 마그네슘을 침전-회수할 수 있는 효율적인 기술이다. 이러한 전해 반응 기술은 주로 양이온교환막, 음이온교환막, 전기투석, 비막 방식 등으로 분류된다. 가장 보편적인 양이온교환막 기반 전해공정은 음극액 내 수산화이온 이동을 억제하여 효과적인 수산화마그네슘 침전을 촉진한다. 또한 탈기나 침전공정의 다단화 등을 통해 마그네슘 이온의 회수 효율성 및 선택성을 높이고 순도 높은 마그네슘 생산이 가능하다. 한편, 음이온교환막을 이용한 최근 연구는 염화마그네슘이 포함된 염수 음극액으로 고농도 이산화탄소를 흡수시키는 데 중점을 두었으며 음이온 교환막은 음극액 내 염소를 이동시키고 양극액 내 수소이온의 이동을 억제하여 이산화탄소의 흡수를 증진시키는 역할을 한다. 흡수된 이산화탄소는 마그네슘과 결합하여 수산화마그네슘을 탄산마그네슘으로 전환시키는 역할을 한다. 선택적 전기투석 방식은 다중막 기반, 다소 마그네슘 농도가 낮은 해수를 탈염시키고 마그네슘을 여타 음이온이나 1가 양이온 대비 선택 농축시키는 장점이 있는데, 다중막 이용에 대한 비용 등 효과 대비 경제성을 평가하고 관련 문제를 해결해 나가야 될 것으로 본다. 마지막으로 비막 방식은 이온교환막 없이 직접 전해를 통해 마그네슘을 회수하는데, 전통적인 전해 반응 기술에 비해 비용이 저렴하고 운영이 간편하다는 장점이 있으나 아직 기초 단계로 순도 및 효율을 최적화하기 위한 연구가 더 필요할 것으로 보인다.
최근 관련 연구 동향은 고농도 마그네슘 함유 해수나 염수를 사용하여 전해조에서 수산화 마그네슘을 선택 회수하는 것으로 집중되며, 일반 해수를 사용할 경우에도 회수의 효율성 선택성이 높아질 것으로 기대된다. 또한, 향후 스케일업 시스템의 장기운전을 통해 해수나 염수 시료를 사용하여 가능한 다양한 유가물질에 대한 선택적 고효율 회수의 최적화와 더불어 기존 유사 기술 대비 경제성 및 환경성을 증진시키는 것이 중요하다. 최적화 및 경제성 평가 시 특히 막의 수명 및 교체주기를 고려하여 현실적인 운전비용을 고려해야 한다. 또한 액중 과포화도 등 다양한 인자에 대한 모니터링 데이터를 기반으로 실용적인 공정 모델링이 필요하다고 본다.