1. 서 론
2. 실험 방법
3. 결과 및 고찰
3.1. 생석회 원료의 기초 특성 분석
3.2. 건식수화 소석회 제조공정 최적 조건 연구
3.3. 건식수화 소석회 제조공정 전처리 및 후처리 개선 연구
3.4. 최적 건식수화공정에 의해 제조된 소석회의 특성 분석
4. 결 론
1. 서 론
소석회(Ca(OH)2)는 다양한 산업 분야에서 필수적인 화학물질로 사용되며, 특히 환경 처리, 건축 재료, 화학 합성 및 제철 공정 등에서 그 수요가 꾸준히 증가하고 있다. 소석회의 성능은 주로 비표면적, 입도 분포, 세공용적과 같은 물리적·화학적 특성에 크게 좌우되며, 이러한 특성은 제조 공정 조건에 따라 크게 달라진다. 특히, 소석회의 세공용적과 SO2 흡수율은 비례관계에 있으며, 세공용적이 클수록 더 높은 SOx 제거 효율을 보이는 것으로 보고되었다1). 따라서, 고품질의 소석회를 효율적으로 생산하기 위한 최적화된 공정 개발이 중요한 과제로 여겨진다. 배연탈황(Flue Gas Desulfurization, FGD)은 화력발전소 및 산업시설에서 배출되는 SOx를 제거하기 위한 대표적인 환경공정으로, 소석회는 이 과정에서 핵심적인 역할을 한다. 특히 습식 FGD 공정에서는 소석회가 SOx와 반응하여 황산칼슘(CaSO4·2H2O)을 형성하며, 이때 소석회의 비표면적과 세공 구조는 반응 속도와 제거 효율을 결정짓는 중요한 요인으로 작용한다. 연구에 따르면, 소석회의 비표면적이 증가할수록 반응 접촉 면적이 확대되어 SOx 제거 효율이 크게 향상된다2). 또한, 적절한 세공 구조는 SOx의 확산을 원활하게 하고, 반응 부산물의 생성으로 인한 세공 막힘을 방지하여 지속적인 효율성을 유지하는 데 기여한다. 소석회는 생석회(CaO)와 물(H2O)의 반응을 통해 생성되며, 이 과정에서 생석회 대비 물 비율(W/CaO), 반응 온도, 그리고 첨가제의 종류 및 농도가 결정 구조와 입도 분포에 중요한 영향을 미친다. 특히, 수화 반응 중 발생하는 비균질한 반응 속도는 Ca(OH)2 결정 크기의 불균일성과 세공 구조의 비효율성을 유발하여 소석회의 비표면적과 기능적 활용성을 저하시킨다. 따라서, 반응을 제어하고 균질한 물리적 특성을 가진 소석회를 생산하기 위한 연구가 필요하다. 다양한 첨가제 중에서 디에틸렌글리콜(Diethylene glycol)은 소석회의 비표면적과 세공 특성을 향상시키는 데 효과적이며, 이를 통해 SOx 흡수율을 기존보다 약 20 % 이상 개선할 수 있는 것으로 기존 연구에서 보고되었다3). 디에틸렌글리콜를 이용한 소석회의 비표면적은 최대 60 m2/g까지 달성 가능하며, 세공용적이 0.2 cm3/g 이상 유지되면 SOx 흡수 효율이 크게 증가하는 경향을 보인다. 또한, 10 nm 정도의 세공 구조를 형성하면 SOx 흡수 속도와 효율이 각각 최대 70 % 이상으로 증가하며, 특정 조건에서는 제거 효율이 거의 100 %에 달할 수 있는 것으로 알려져 있다3).
본 연구에서는 고 비표면적과 균일한 입도 분포를 가진 소석회를 제조하기 위한 최적 공정을 제시하고자 하였다. 이를 위해 생석회의 전처리, 수화 반응 조건, 에틸렌글리콜 첨가 효과, 그리고 후처리 조건을 체계적으로 분석하였다. 특히, Ca(OH)2 결정 크기, 비표면적, 그리고 세공 구조를 분석하고, 에너지 효율성과 공정 적합성을 고려한 최적의 제조 조건을 제안하는 데 중점을 두었다. 이를 통해, 산업적으로 활용 가능한 고품질 소석회 제조 공정을 개발하고, 다양한 응용 분야에서의 효율적 활용 가능성을 확대함과 동시에 배연탈황 공정에서의 환경적 기여를 강화하고자 한다.
2. 실험 방법
본 연구에서는 실제 산업에서 제조 및 판매되고 있는 생석회를 사용하였다. 일반적으로 생석회는 미반응 CaCO3를 포함하고 있어 소석회 제조 시 불순물로 작용할 수 있으므로, 이를 제거하기 위한 전처리 과정을 거쳤다. 전처리는 죠 크러셔(Jaw crusher) 및 해머 밀(Hammer mill)을 이용하여 1 mm 이하로 파쇄한 후, 200 mesh 또는 325 mesh 체로 체질하여 실험에 사용하였다. 소석회의 반응성을 제어하기 위해 유기질 분산제로는 시약급의 에틸렌글리콜(ethylene glycol)을 사용하였다. 실험에 사용된 공정 변수는 Table 1에 요약되어 있으며, W/CaO = 0.5, 0.6, 0.9 로 설정하였다. 분산제인 에틸렌글리콜의 첨가량은 1, 4, 8 %로 조절하였다. 주 용매로는 3차 탈 이온수를 사용하였으며, 용매의 온도는 25, 45, 65, 85 ± 1 ℃로 제어하여 반응 실험 단계에서 투입하였다. 혼합은 특별한 장비를 사용하지 않고 시약수저로 혼합을 진행하였으며, 수화 시간은 최대 30 분으로 제한하였다. 혼합한 시료는 실온(23 ± 1 ℃)에서 24 시간 숙성시키고, 105 ℃에서 24 시간 동안 건조하였다. 이후, 흡착된 수분의 2 차 반응을 방지하고 완전 증발을 유도하기 위해 200 ℃에서 24 시간 건조와 Ca(OH)2 탈수 온도 이하인 350 ℃에서 30 분간 건조를 병행하여 수행하였다4). 소석회 제조를 위한 실험 공정도를 Fig. 1에 나타내었다.
또한, 비표면적을 향상시키기 위해 에틸렌글리콜을 생석회 미분말과 직접 건식혼합하는 새로운 전처리 공정을 도입하였다. 건식혼합은 20 L 용량의 볼밀을 사용하여 혼합을 진행하였으며, 볼 크기 및 투입량은 36.5 mm 87개, 30.2 mm 134개, 25.4 mm 20개, 19.1 mm 142개, 15.9 mm 188개를 투입하였다. 볼밀의 회전수는 분당 70 rpm으로 설정하였다. 이러한 전처리 공정을 도입한 실험은 기존 공정과의 비교분석을 위해 상기에 서술한 시험법의 혼합 공정에 선행하여 수행하였다.
Table 1.
Process variables for the preparation of calcium hydroxide
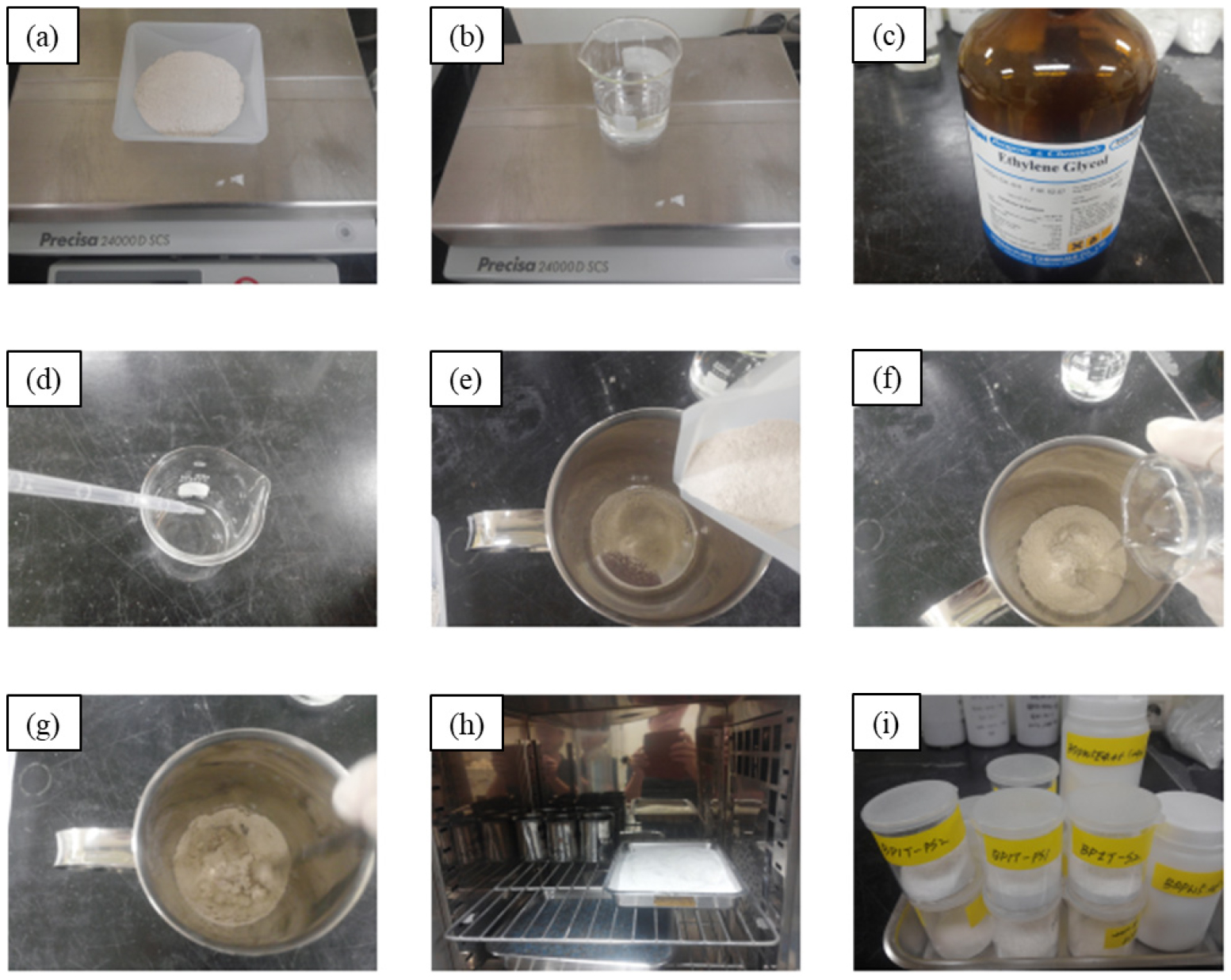
Fig. 1.
Experimental procedure for hydrated lime preparation (a) weighing quicklime, (b) weighing water, (c) preparing ethylene glycol, (d) mixing ethylene glycol using the wet method, (e) adding the powdered material, (f) adding the solvent, (g) performing the mixing process, (h) drying the mixture, and (i) sampling and storage.
제조한 소석회의 비표면적과 세공용적 분석은 ASAP 2020(Micromeritics corp. USA) 장비를 사용하여 측정하였다. N2 가스 흡착량을 측정하여 고체의 총 비표면적(Brunauer–Emmett–Teller)과 세공용적(Barrett–Joyner–Halenda)을 측정하였다. 소석회의 입도분포 측정은 LS 13320(Beckman Coulter Corp., Turkey)을 사용한 습식 방법으로 진행하였으며, 용매로 에틸 알코올(ethyl alcohol)을 사용하였다. 탈황 성능은 ASTM C1318-95(FGD)에 기반한 습식법으로 평가하였다. 총 중화능력 평가를 위한 염산 적정법은 ASTM C1318-95에 기반하여 수행하였으며, 비교군으로 국내 B社의 공업용 소석회를 사용하였다. 염산 적정법에 사용된 염산은 1 N 농도로 제조하였고, 소석회 1.402 g와 증류수 50 mL를 혼합하여 교반한 후, 수동 적정 장치를 통해 pH 6 ± 0.4에 도달할 때까지 30분 동안 적정하였다. 이 과정에서 사용된 염산의 양을 기준으로 총 중화능력(Total Neutralizing Capability, TNC % as CaO)을 평가하였다(Table 2). 실험은 용해 반응조, 수용액상의 산 공급 장치, pH 측정 및 조절 장치 등을 포함한 동일한 실험 장비에서 수행되었으며, 실험실의 온도(20 ± 2 ℃)와 습도(50 ± 10 %)를 일정하게 유지하여 환경적 영향을 최소화하였다. 실험 데이터는 재현성을 확보하기 위해 동일한 조건에서 3 회 반복 실험한 결과의 평균값으로 산출하였다. 광물상 및 결정입자 크기 분석을 위하여 X선 회절 분석장비(D/MAX-2500/PC, Rigaku corp. Japan)를 이용하였다. 스캔 속도: 2 °/min, 측정범위 10 – 65 °, Cu-Kα: 40 kV, 30 mA으로 설정하였다. 소석회 결정의 크기를 산정하기 위하여 측정된 XRD 분석결과를 토대로 (101)면 (d = 0.264 nm)의 피크에 대해 반가폭을 측정하고, 탄산칼슘의 (112)면 (d = 0.262 nm) 피크를 보정용으로 이용하여 결정격자의 크기를 계산하였다.
D = 입자의 평균 직경(nm)
λ = X선 회절 장치의 Cu-Kα 파장: 0.154 nm
β0 = 확산한 회절선의 반가폭(rad)
βe = 같은 위치의 양호한 결정의 반가폭(rad)
θ = 측정에 이용한 2 θ 각의 절반(rad)
Table 2.
Titration method based on ASTM C1318-95
3. 결과 및 고찰
3.1. 생석회 원료의 기초 특성 분석
실험에 사용한 생석회의 원료 특성을 분석하기 위해 X선 회절분석(XRD)을 수행하였다(Fig. 2). 분석 결과, 원료는 대부분 칼슘 기반의 광물상(CaO, JCPDS No. 37-1497)을 나타냈으나, 토중로의 특성으로 인해 미 소성된 방해석(CaCO3, JCPDS No. 47-1743)가 상당량 포함되어 있는 것으로 확인되었다. 이러한 미반응 CaCO3는 소석회 제조 과정에서 제품의 물리적, 화학적 특성에 부정적인 영향을 미칠 가능성이 있기 때문에, 이를 효과적으로 제거하기 위한 전처리 공정을 수행하였다. 전처리 공정은 죠 크러셔와 해머 밀을 활용하여 원료를 1 mm 이하의 크기로 분쇄한 후, 200 mesh 또는 325 mesh 체를 이용하여 체질하여 실험에 사용하였다. 체질 생석회 시료에서 미반응 CaCO3의 피크가 감소하였으며, 이는 분쇄 및 체질 과정에서 미 소성된 방해석 입자가 상대적으로 큰 입자 크기로 존재하여 체질 시 제거되었기 때문으로 판단된다. 따라서, 전처리를 통해 생석회의 품질 저하 요인을 일부 제거할 수 있음을 확인하였다.
3.2. 건식수화 소석회 제조공정 최적 조건 연구
일반적으로 괴상의 생석회를 이용하여 소석회 제조 시에는 생석회의 표면에서의 내부까지 완전히 수화가 완료되는 속도가 상이하여 Ca(OH)2 결정형태가 불균질하게 형성된다. 이로 인해 세공 또한 불균질하게 되어 비표면적이 높은 소석회를 제조하기에 부적절하다. 따라서, 1 mm 이하 크기로 파 분쇄한 생석회를 사용하여 소석회 제조실험을 진행하였고, 분산제의 첨가량, 적정 물의 온도 및 물 온도에 대한 최적조건 범위를 도출하고자 하였다. 또한, 생석회의 파 분쇄별 시료 외관 사진을 나타내었다(Fig. 3).
3.2.1. 1 mm 이하 크기의 생석회 활용 소석회 제조
1 mm 이하 크기의 생석회를 활용하여 제조한 소석회의 제조 조건별 비표면적을 측정하였다(Fig. 4). 에틸렌글리콜이 첨가되지 않은 실험 조건에서 물 온도가 증가함에 따라서 비표면적도 증가하는 경향을 나타내었다. 그러나, 25 ℃에서 85 ℃로 물의 온도가 상승함에 따라 비표면적이 증가하기는 결과를 보이지만, 증가량은 높지 않았으며 적정 온도는 45 ℃인 것으로 판단된다. 이러한 결과는 물의 온도가 수화 반응 속도와 결정 형성에 영향을 미치기 때문으로 판단된다. 물의 온도가 상승하면 생석회와 물의 반응 속도가 빨라지고, 이는 Ca(OH)2 결정의 형성과 다공성 구조의 발달을 촉진하여 비표면적을 증가시키는 주요 요인으로 작용한다. 또한, 높은 용매 온도에서는 반응물의 확산이 원활해지고, 생성된 Ca(OH)2 입자의 균일한 분산을 유도하여 고 비표면적 구조를 형성한다. 그러나 45 ℃ 이상으로 온도를 높였을 때 비표면적 증가량이 제한적인 이유는, 과도한 용매 온도가 결정의 응집 및 성장을 유발하여 입자의 다공성을 감소시킬 수 있기 때문이다5).
에틸렌글리콜 첨가량에 따른 비표면적 측정 결과, 용매 온도 25 – 65 ℃ 범위에서 에틸렌글리콜의 함량이 증가할수록 비표면적도 증가하는 경향을 보였다. W/CaO = 0.5, 용매 온도 45 ℃ 인 조건에서, 에틸렌글리콜 함량의 증가에 따라 비표면적이 증가하였으며, 에틸렌글리콜 첨가량 8 %에서 최대 17.84 m²/g의 비표면적이 관찰되었다. W/CaO = 0.6, 용매 온도 45 ℃ 조건에서는 에틸렌글리콜 8 % 첨가 시 비표면적이 최대 19.98 m²/g까지 증가하는 결과를 얻었다. 이러한 결과는 에틸렌글리콜이 수화 반응 과정에서 표면 활성제로 작용하여 Ca(OH)2 입자의 형성과정에서 입자 간 응집을 억제하고, 균일한 분산을 유도했기 때문으로 판단된다6). 이는 입자의 다공성 구조 형성을 촉진하여 비표면적을 증가시키는 중요한 요인으로 작용한다. 하지만, 에틸렌글리콜 첨가량이 8 %, 용매 온도 85 ℃인 시료의 경우 비표면적이 감소하는 결과를 확인할 수 있었다. 이는 에틸렌글리콜이 첨가되었을 때 과도한 용매 온도에 의해 Ca(OH)2 결정의 표면에 과잉 흡착이 발생하여 반응 물질(H2O, CaO)의 접근을 방해하거나, 이미 억제된 결정 성장 이상의 추가적인 효과를 기대하기 어려워지기 때문이다. 또한, 에틸렌글리콜의 과도한 첨가는 경제적 효율성 측면에서도 불리하다. 결론적으로, 에틸렌글리콜 함량이 4 %에서 비표면적이 15 - 17 m²/g로 안정적으로 유지되는 것은 에틸렌글리콜의 표면 활성 효과와 결정 성장 억제 효과가 적정 수준에서 균형을 이루었기 때문으로 해석된다.
따라서, W/CaO, 에틸렌글리콜 첨가량, 용매 온도 및 에너지 효율을 고려하여 적정 조건을 W/CaO = 0.5, 에틸렌글리콜 첨가량 4 %, 용매 온도 45 ℃로 선정하였다.
3.2.2. 200 mesh 이하 미분쇄 생석회 활용 소석회 제조
1 mm 이하 크기의 생석회를 사용하여 소석회를 제조한 결과 높은 비표면적(30 m2/g 이상)을 얻을 수 없었다. 따라서, 불순물 함량을 줄이고 반응속도를 더욱 균질하게 하기 위해서 200 mesh 체를 통과한 시료를 이용하여 소석회를 제조하였다. 소석회 제조 조건은 이전 실험에서 최적화된 W/CaO = 0.5, 용매 온도 45 ℃를 설정하였고, 에틸렌글리콜 첨가량(0, 4, 8 %)을 공정 변수로 제어하였다. 이때, 1 %의 에틸렌글리콜 첨가량은 에틸렌글리콜에 의한 비표면적 향상을 최대화 할 수 없다는 것을 1 mm 이하 크기의 생석회를 사용한 실험 결과에서 확인했기 때문에 1 % 조건을 제외하고 0, 4, 8 %의 첨가량을 공정 변수로 설정하였다.
200 mesh 이하 크기의 생석회 시료를 사용하여 에틸렌글리콜을 4, 8 % 첨가에 따른 비표면적 측정 결과 24.0 m2/g 및 23.8 m2/g으로 함량에 따른 비표면적 증대 효과는 거의 없는 것을 알 수 있었다(Fig. 5). 325 mesh 이하로 더 미세한 입도의 생석회를 사용하여 소석회를 제조한 결과, 200 mesh 이하 시료를 사용했을 때와 유사한 비표면적 결과를 보였다. 325 mesh 크기의 생석회를 사용하고, 에틸렌글리콜 4 %를 첨가한 경우 비표면적은 24.5 m2/g로 나타났고, 에틸렌글리콜을 8 % 첨가했을 경우 24.2 m2/g으로 나타났다. 이러한 결과는 추가적인 분쇄 과정을 통해 얻어진 325 mesh 이하의 미세한 입도가 비표면적 증대에 미치는 영향이 제한적이며, 입자가 미세해질수록 물과 반응할 수 있는 표면적이 증가함에도 불구하고 200 mesh 이하 입자 크기에서 이미 충분한 반응 표면적이 확보되었기 때문으로 판단된다. 또한, 미세한 입도를 지니는 분말은 반응 중 입자 간 뭉침(agglomeration) 현상을 일으켜 비표면적 증가 효과를 제한했을 가능성이 있기 때문으로 판단된다.
추가적으로, 325 mesh 크기의 생석회를 사용하고 W/CaO = 0.9로 설정하여 제조한 소석회의 비표면적은 25.1 m²/g로 증가하였다. 그러나, W/CaO = 0.9까지 증가시킨 경우, W/CaO = 0.5일 때에 비해 입자 간 상호 응집이 심화되는 결과를 나타냈다(Fig. 6). 이러한 응집 현상을 해결하기 위해 추가적인 파쇄 및 분쇄 공정이 필요하기 때문에 분쇄 에너지 효율성과 공정 적합성을 고려했을 때 200 mesh 이하 크기의 생석회를 활용하는 것이 가장 적합할 것으로 판단된다.
3.3. 건식수화 소석회 제조공정 전처리 및 후처리 개선 연구
본 연구에서는 소석회의 비표면적을 30 m2/g 이상으로 증가시키기 위해 전처리 및 후처리 방법을 개선하는 방법을 도입하였다. 초기 실험에서는 기존의 에틸렌글리콜 첨가 방식을 활용한 습식혼합 공정을 적용했으나, 목표 비표면적에 도달하지 못하는 결과를 얻었다. 이에 따라, 에틸렌글리콜을 생석회 미분말과 직접 건식혼합하는 새로운 혼합 방법을 도입하였다. 건식혼합 전처리 공정을 통해 7 분 이상 혼합한 결과 응집 없이 균일하게 혼합되는 것을 확인할 수 있었다(Fig. 7).
후처리 방법에서도 개선을 시도하였으며, 후처리의 핵심 요소인 숙성 시간(curing time)과 건조 온도를 최적화하여 진행하였다. 숙성 시간이 지나치게 길어질 경우 입자와 입자 또는 결정과 결정 사이에 흡착된 수분이 2차 결정 성장 반응을 일으켜 세공 구조가 치밀해지고 비표면적이 감소하는 것으로 판단된다. 이를 방지하기 위해 수화 시간을 최대 30 분으로 제한하였다. 비표면적 측정 결과 혼합 방식을 습식으로 적용한 경우 350 ℃ 건조에서 일부 효과가 있었으나 비표면적 30 m2/g에 도달하지 못하였다(Table 3). 반면, 건식혼합 방식으로 제조된 시료를 200 ℃ 및 350 ℃ 건조한 결과 모두 비표면적 30 m2/g 이상을 달성하였으며, 각각 최대 31.8 m2/g 및 39.1 m2/g의 비표면적을 보유하였다. 또한, 30 m2/g 이상을 달성한 조건에 대한 재현성을 평가하기 위해 각 조건에서 3 회 반복 실험 결과를 통해 재현성을 확인하였다. 최종적으로 에너지 효율성과 공정 적합성을 고려하여 200 mesh 이하 크기의 생석회, W/CaO = 0.5, 물 온도 45 ℃, 에틸렌글리콜 첨가량 4 %, 건식혼합, 건조 조건 350 ℃가 최적 조건으로 도출되었다.
Table 3.
Specific surface area of calcium hydroxide based on pretreatment (mixing method) and post-treatment (drying method)
3.4. 최적 건식수화공정에 의해 제조된 소석회의 특성 분석
3.4.1. 에틸렌글리콜 첨가에 따른 Ca(OH)2 결정 크기와 입도 분포 분석
200 mesh 이하 크기의 생석회를 사용하여 본 연구에서 도출된 최적 건식수화공정 조건(W/CaO = 0.5, 용매 온도: 45 ℃)을 적용하고, 에틸렌글리콜 함량을 변수로 하여 제조한 소석회의 입도분포 결과를 나타내었다(Fig. 8). 그림에서와 같이 에틸렌글리콜 첨가에 따라 전체적인 입도가 감소하는 경향을 확인 할 수 있다. 에틸렌글리콜을 첨가하지 않은 경우 10.2 μm의 평균입도를 보였으며 4 % 혼입 시 5.5 μm, 8 % 혼입 시에는 다소 증가하는 6.1 μm의 평균입도를 나타내었다. 에틸렌글리콜 혼합에 따라 입도는 감소되는 경향을 보이지만, 함량차이에 따른 변화는 크지 않는 것으로 나타났다.
이러한 결과는 생성되는 Ca(OH)2 입자의 결정크기와 비교하여 설명될 수 있으며, XRD 분석을 통하여 계산된 Ca(OH)2 결정의 크기는 다음과 같다(Fig. 9). 에틸렌글리콜이 첨가되지 않았을 경우 39.6 nm의 결정 크기를 보였으며, 4 % 첨가 시 26.1 nm, 8 % 첨가 시 25.5 nm를 나타내어 에틸렌글리콜의 첨가에 따라 30 % 이상 결정의 크기가 작아지는 것을 확인하였다. 이러한 결과는 에틸렌글리콜을 첨가하지 않았을 경우는 전체적으로 반응속도가 불균질하게 진행되는 것으로 보이는데, 파분쇄된 생석회를 활용함에 따라 미분말 부분이 먼저 반응이 진행되고 다소 큰 입자들은 아직 반응이 시작되지 않는 부분이 있어 균일한 입도의 소석회가 생성되지 못하는 것으로 판단된다. 그러나, 에틸렌글리콜 첨가 시 전체적인 반응 속도를 지연시켜 최대한 전체 생석회 시료에 물이 충분히 침투될 수 있는 시간을 제공함으로서 반응이 전체적으로 균일하게 일어나기 때문에 생성되는 소석회 입자 분포 또한 균질하게 확보되는 것으로 판단된다.
3.4.2. 소각제 배가스의 SOx 제거 효율 결과
본 연구에서 제조된 두 가지 고기능성 소석회의 총 중화 용량(TNC) 결과를 나타내었다(Table 4). 2번 샘플은 약 24 m2/g의 비표면적을 가진 반면, 샘플 4는 30 m2/g 이상의 비표면적을 가지는 소석회 샘플이다. 실험의 신뢰성을 보장하기 위해 각 샘플에 대해 3 회 반복 실험을 진행하였으며, 평균값을 산출하였다. 두 샘플의 초기 pH는 12.62 - 12.77로 강한 알칼리성을 나타내었다. 적정 장치를 사용하여 30 분 동안 pH 6 ± 0.4를 유지하기 위해 필요한 염산(HCl) 첨가량은 두 샘플 모두 유사한 경향을 보였으며, 계산된 TNC 값은 61.2142 %와 65.6706 %로 측정되었다. 비표면적이 상대적으로 낮은 2번 소석회 샘플(24 m2/g)에 비해 비표면적이 30 m2/g 이상인 4번 샘플은 TNC가 약 4 % 증가하며 중화 용량이 크게 향상된 것으로 나타났다. 이는 중화 효율 향상에 있어 비표면적의 중요성을 입증하는 결과이다. 중화 용량의 차이는 소석회의 물에 대한 용해 속도와 밀접하게 연관되어 있으며, 비표면적이 증가함에 따라 수용액 내에서 반응 표면의 노출이 증가하여 용해가 가속화되고 반응성이 향상되기 때문인 것으로 판단된다7). 또한, 비표면적이 큰 소석회는 물과의 접촉 면적이 확대되어 반응물(H⁺, Ca(OH)2)이 접촉할 수 있는 활성 부위가 증가할 수 있다. 일반적으로 소석회의 물에 대한 용해도는 비표면적이 커질수록 증가하는 경향을 보이며, 이는 반응 효율 향상의 핵심 요인으로 작용한다. 예를 들어, 20 ℃에서 소석회의 용해도는 약 0.173 g / 100 mL로 보고되어 있으며, 비표면적 증가 시 더욱 빠른 용해 속도를 나타낸다. 결론적으로, 소석회의 비표면적 증가가 중화 용량(TNC)과 반응 효율에 미치는 긍정적인 영향을 확인 할 수 있었다. 비표면적이 큰 소석회는 물과의 접촉 면적이 증가하고 반응 속도가 가속화됨으로써, SOx와 같은 유해 가스의 제거 효율을 극대화할 수 있음을 보여준다. 이러한 결과는 고기능성 소석회의 활용이 환경 오염 물질 저감 기술에서 중요한 역할을 할 수 있음을 시사하며, 특히 SOx 제어와 같은 산업 응용에서 비표면적의 조절이 필수적인 설계 요소로 작용할 가능성을 제시한다.
향후 연구에서는 비표면적 외에도 소석회의 결정 구조와 화학적 조성이 중화 효율에 미치는 영향을 다각적으로 분석하여, 더욱 향상된 성능의 소석회 소재를 개발할 수 있는 과학적 기반을 마련할 필요가 있다.
Table 4.
Total Neutralizing Capacity Results According to ASTM C1318-95
4. 결 론
본 연구는 소석회의 비표면적과 세공 부피를 증가시키면 반응성과 중화 능력이 크게 향상되어 배연 탈황과 같은 응용 분야에서 더욱 효과적으로 활용될 수 있음을 입증하였다. 실험 결과, 본 연구에서 제조된 소석회는 최대 비표면적 39.1 m2/g과 세공 부피 0.177 cm3/g를 달성하였다. 이는 전처리, 수화 공정 조건, 후처리 개선을 통해 얻어진 결과로, 고성능 소석회 제조에 필수적인 요소임을 확인하였다.
최적 조건으로는 생석회를 1 mm 이하로 분쇄하고, 200 mesh 이하로 체질한 후, W/CaO = 0.5, 수화 온도 45 ℃, 에틸렌글리콜 첨가량 4 %를 적용한 공정이 가장 우수한 결과를 보였다. 특히, 후처리 단계에서 350 ℃에서 30 분간 건조하는 조건이 비표면적 증가에 가장 효과적이었다. 이러한 최적화된 공정은 소석회의 비표면적과 세공 구조를 극대화하여 반응성과 중화 능력을 개선하였다. 비표면적이 30 m2/g 이상인 소석회 시료는 24 m2/g 시료에 비해 총 중화능력(TNC)이 약 4 % 증가하였다. 이러한 결과는 높은 비표면적과 최적화된 세공 구조를 가진 소석회가 SOx 제거 효율을 극대화할 수 있다는 결과와 일치한다.
결론적으로, 본 연구는 FGD와 같은 산업적 응용 분야의 요구를 충족시키기 위해 소석회의 비표면적과 세공 구조를 증가시키는 실질적이고 효과적인 공정을 확립하였다.